Химико-термическая обработка инструмента NOX
Содержание
1. Как происходит процесс карбонитрации?
Введение
Одна из главных задач инструментального производства – изготовить режущий инструмент, который имеет высокую износостойкость в процессе эксплуатации. Решение этой задачи обеспечивается за счет:
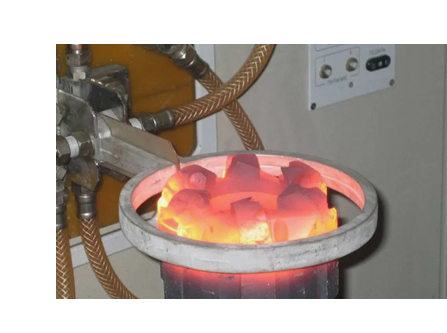
- повышения физико-механических свойств материала рабочей части инструмента;
- оптимизации конструкции рабочей части инструмента;
- оптимизации структуры материала в процессе операции основной термической обработки.
Кроме того, в современном инструментальном производстве применяют широкий спектр технологий, обеспечивающих дополнительное упрочнение поверхностного слоя материала. Одной из таких технологий является технология химико-термической обработки (ХТО). Методы ХТО основаны на комбинированном тепловом и химическом воздействии на металл, обеспечивающем управляемое изменение физико-механических и физико-химических свойств поверхностного слоя изделия (микротвердости, теплостойкости, адгезионной активности, усталостной прочности и т. п.).
Среди многообразия методов химико-термической обработки выделяется оксикарбонитрация (NOX). Оксикарбонитрация– эффективный процесс упрочнения поверхности корпусов фрез и державок за счёт насыщения её атомарным азотом и углеродом в расплаве солей.
Как происходит процесс карбонитрации?
Источниками диффундирующих в инструментальный материал элементов являются газы, жидкости и твердые материалы. При ХТО производят диффузионное насыщение поверхностного слоя металлов азотом, углеродом, а также бором, хромом, алюминием, молибденом, серой, фосфором и др. Глубина насыщенного слоя зависит от температуры, времени насыщения и концентрации диффундирующего элемента.
Наиболее эффективной технологией является ионно-плазменное азотирование, производимое в плазме тлеющего разряда. Насыщение поверхностного слоя металла инструмента ионами азота (а не атомами, как при других методах азотирования) происходит в среде аммиака или азота в условиях сильной ионизации газа за счет создания электрического потенциала напряжением 400…1000 В. Инструмент подсоединяют к катоду, а корпус рабочей камеры служит анодом. Если инструмент имеет сложную форму, то изготавливают специальный профилированный анод. Между электродами возбуждают тлеющий разряд, при этом ионы азотсодержащего газа бомбардируют катод и нагревают его до температуры насыщения азотом.
Продолжительность операции примерно 1…1,5 часа. Толщина легированного азотом слоя составляет 10…80 мкм, а твердость достигает HRC 70. Азотированный поверхностный слой, обладая высокой твердостью, имеет недостаток – повышенную хрупкость. Для ее снижения применяют технологии азотирования в комбинированной среде, содержащей азот и углерод. Углерод уменьшает долю азота в поверхностном слое и обеспечивает лучшие эксплуатационные свойства готового изделия.
Наиболее эффективной технологией является ионно-плазменное азотирование, производимое в плазме тлеющего разряда. Насыщение поверхностного слоя металла инструмента ионами азота (а не атомами, как при других методах азотирования) происходит в среде аммиака или азота в условиях сильной ионизации газа за счет создания электрического потенциала напряжением 400…1000 В. Инструмент подсоединяют к катоду, а корпус рабочей камеры служит анодом. Если инструмент имеет сложную форму, то изготавливают специальный профилированный анод. Между электродами возбуждают тлеющий разряд, при этом ионы азотсодержащего газа бомбардируют катод и нагревают его до температуры насыщения азотом.
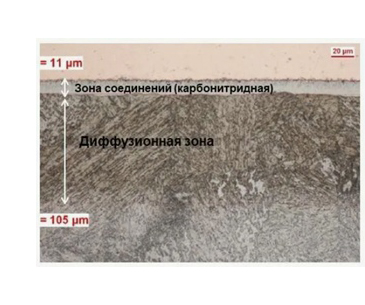
Продолжительность операции примерно 1…1,5 часа. Толщина легированного азотом слоя составляет 10…80 мкм, а твердость достигает HRC 70. Азотированный поверхностный слой, обладая высокой твердостью, имеет недостаток – повышенную хрупкость. Для ее снижения применяют технологии азотирования в комбинированной среде, содержащей азот и углерод. Углерод уменьшает долю азота в поверхностном слое и обеспечивает лучшие эксплуатационные свойства готового изделия.
Для чего нужна оксикарбонитрация?
Эксплуатационная надежность деталей машин в основном определяется способностью их поверхности сопротивляться различным видам износа, коррозии, усталостным разрушениям и др. Это связано с тем, что поверхностные слои деталей нагружены более интенсивно, чем сердцевина, и, соответственно, возникающие напряжения здесь имеют максимальные значения. Это справедливо, в том числе и в отношении металлорежущего инструмента.
Оксикарбонитрация обеспечивает:
- повышение твёрдости поверхности в 2-5 раз;
- повышение износостойкости в 2-10 раз;
- повышение усталостной прочности на 30-80%;
- повышение коррозионной стойкости в 50-200 раз;
- В результате такого уникального сочетания свойств, срок службы инструмента увеличивается в 2-5 раз.
Преимущество применения оксикарбонитрирования от объемной закалки заключается в том, что при проведении процесса мы получаем поверхностную твердость на корпусах до 750 HV при сохранении вязкой внутренней части. В отличие от нанесения покрытия, упрочняется сам материал изделия без нанесения дополнительного слоя, уменьшение твердости идет постепенно в глубь материала без четкой границы твердой и вязкой структуры.
NOX обеспечивает более высокую прочность фрез и уменьшает склонность к возникновению вибраций, тем самым обеспечивая более стабильные условия резания, более высокую точность и качество обрабатываемой поверхности, а также обеспечивает более высокую стойкость пластин.
Компания «Русский Инструмент» производит металлорежущий инструмент c химико-термическом упрочнением NOX. В ассортименте представлены торцевые фрезы серии AF290 и AF245; торцово-цилиндрические серии AH290 и AH190; дисковые фрезы AS290, AS100, а также концевые фрезы AF290
Получите консультацию, связавшись со специалистами компании «Русский Инструмент»!
Товары